GE iSTAT i400 Mean Sensing (i4CA, i4VA), DC (i4Dx) Transducers and i4XS Communications Interface
iSTAT i400
Mean Sensing (i4CA, i4VA), DC (i4Dx) Transducers and i4XS Communications Interface
The iSTAT i400 range of Mean Sensing AC transducers, DC transducers and communications interface provide easy installation and commissioning as well as simple and economical monitoring and communications. The iSTAT i400 Mean Sensing and DC transducers are simple and compact offerings available to measure AC or DC circuits respectively for utility and industrial applications.
The self-powered, i400 Mean Sensing AC transducers (i4CA, i4VA) are used to measure current or voltage and provide an output analogue signal as an indication.
The iSTAT i400 DC measuring transducers monitor values such as DC Volts (i4DB), DC Current (i4DC), Tap Position (i4DA), Resistance (i4DF), and Temperature (Resistance Temperature Detector) (i4DG) and provides an analogue output or communications. The i400 i4Dx DC measuring transducers also provide Modbus serial communications for integration into monitoring systems.
The iSTAT i4XS communications interface provides a Serial to Ethernet interface allowing easy connection and integration of devices to a communications network and monitoring system.
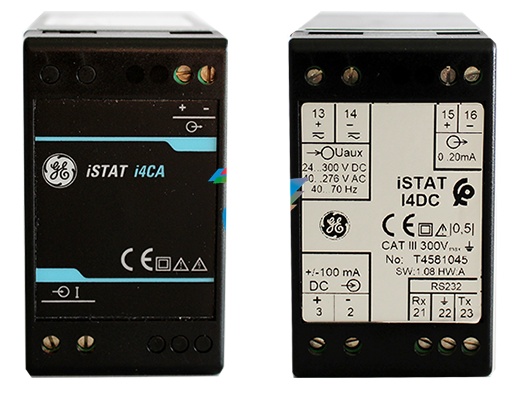