GE Multilin D.20 I/O Modules
Multilin D.20 I/O Modules
GE’s classic D.20 I/O Modules are input/output modules for substation automation and SCADA RTU applications. They have stood the test of time, continue to be widely used, and are extremely reliable. Connecting to G100. G500. D400 (with D.20 RIO), and D20MX, the D.20 I/O Modules provide local, remote, and distributed physical I/O capabilities for digital and DC analog data collection and substation control.
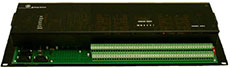
D20 I/O options
A complete family of substation hardened I/O modules makes the G100. G500 or D20MX controller scalable to both large and small substations. A distributed architecture with both ring and star topologies allows for easy expandability and remote placement of I/O modules. The following I/O modules are available in a variety of models with I/O ranges up to 300VDC.
Buy Now D20S – 64 channel status input module
Buy Now D20A – 32 channel DC Analog input module
Buy Now D20K – 32 channel control output module
Buy Now D20KI – 8 external interposer relay pairs module
Buy Now D20C – 16 status input, 8 control output, optional 16 DC analog inputs or 8 analog inputs and 8 analog outputs
I/O with DNP Communication
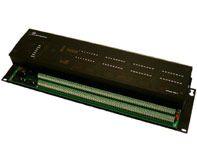
The DNP I/O modules are data collection and control devices that combine the DNP 3.0 communications protocol with our existing industry proven and robust line of I/O modules. The DNP I/O modules implement the industry standard DNP 3.0 (Level 2) slave protocol over a single RS485 interface to provide expandable I/O functionality for the D400. D25 and iBox product lines, as well as third-party products.
The following DNP I/O modules are available:
Buy Now DNPIO-DI (D20S)
Buy Now DNPIO-DCAI (D20A)
Buy Now DNPIO-CO (D20K)
Buy Now DNPIO-C (D20C)
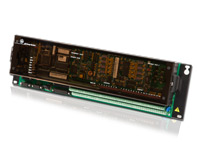